Lean pipe assembly line simply said, it refers to the production of products, through the route. That is, from the raw materials into the production site, after processing, transportation, assembly, inspection and other wake up a series of assembly line activities formed by the route. At the same time, it is also a kind of shelf swing production organization form to complete the product process.
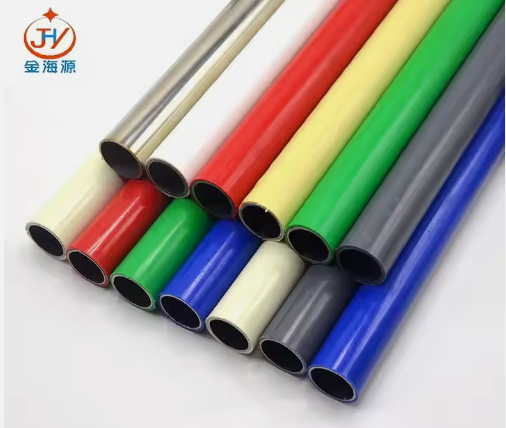
So how should we lean tube pipeline provide efficiency? Firstly, it is improved from the perspective of lean pipe pipeline balance to achieve the existing weekly production tasks, and then the kanban is introduced to further meet the substantial growth of weekly production tasks. After the balance improvement, the cycle time is reduced when only the station operation process is adjusted, the output is increased and the existing weekly driving task is satisfied. In the lean pipeline system, we need to keep every operator responsible for the operation of several machines, which can not only reduce the labor cost but also make the pipeline more flexible to respond to sudden changes.
The product is composed of wire rod and standard connecting accessories, which has the characteristics of convenient disassembly, flexible assembly and improved production efficiency. Suitable for the production and use of many varieties of small batch products. In addition, each station of the lean pipe line maintains synchronization, reduces the differences between each station, make standardized worksheet, stipulate the operation process, reduce unnecessary actions, further shorten the production cycle and improve the production efficiency. Therefore, after the implementation of balanced production, it can further shorten the working time, improve the work efficiency, reduce the waste of working hours, enhance the team consciousness of the staff, but also lay an important foundation for the implementation of lean production.