Lean manufacturing is a method that focuses on minimizing waste while maximizing efficiency and value. Emerging from the Toyota Production System in the 1950s, it has since been adopted by numerous industries worldwide. Going ‘lean’ aims to eliminate various forms of waste, including overproduction, inventory, defects, waiting times, and excessive motion. The ultimate goal is to provide customers with high-quality products in the shortest possible time, at the lowest possible cost.
Lean manufacturing requires adaptability to meet changing customer demands. Tube and bracket systems are inherently modular and can be quickly reconfigured to accommodate new products or process improvements. This flexibility is crucial for staying responsive in a dynamic market.
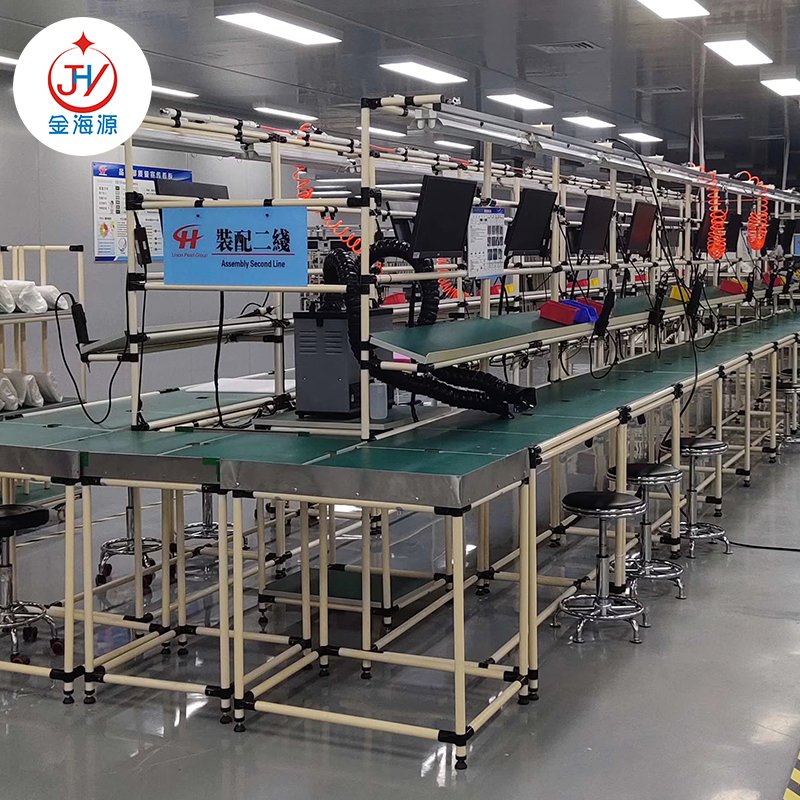
Continuous Flow:
The idea of lean manufacturing emphasizes the continuous flow of materials and information. Tube and bracket systems can be used to design custom flow racks, conveyance systems, and material handling solutions that promote a smooth and uninterrupted production process. This minimizes waiting times and eliminates bottlenecks.
Error Reduction:
Tube and bracket systems help standardize workstations, making it easier for workers to follow standardized work procedures. This reduces the chances of errors and defects, aligning with the lean principle of defect reduction.
Space Optimization:
Lean manufacturing often involves space constraints due to the desire to minimize inventory and workspace. Tube and bracket systems are designed to make the most of available space by allowing vertical storage and efficient space utilization.